HOCHBAU M
in collaboration with Hannes Kofler
|2017|
The main task of the course was to build a large fabrication hall to host a large and at least 3 smaller robots for robot fabrication. The building itself should be build by the robots using a concrete-printing process. As concrete mainly withstands pressure loads, the idea was to use catenarys in order to create the main structure of the building. Between the main structure a second structure is formed to create an outer shell. This shell has openings on its side to get indirect lighting into the fabrication room. The printed structure is divided into parts, which can be printed by the robots without any supporting structure. In a second step holes are drilled into the contact surfaces to ensure a precise connection between the parts, using metalbolts. Although the geometry of the building is almost solely pressure loaded, a fiber-reinforced concrete withstands occurring tension loads. To enclose the working space a foldable glass-facade is applied to the open arches. This glass-panels can be opened to provide an entrance for people and the fork lifter. The openings in the second structure/facade are closed with individual fixed glass-elements. In order to make the glasselements fit precisely into the printed openings, profiles are milled into the concrete.
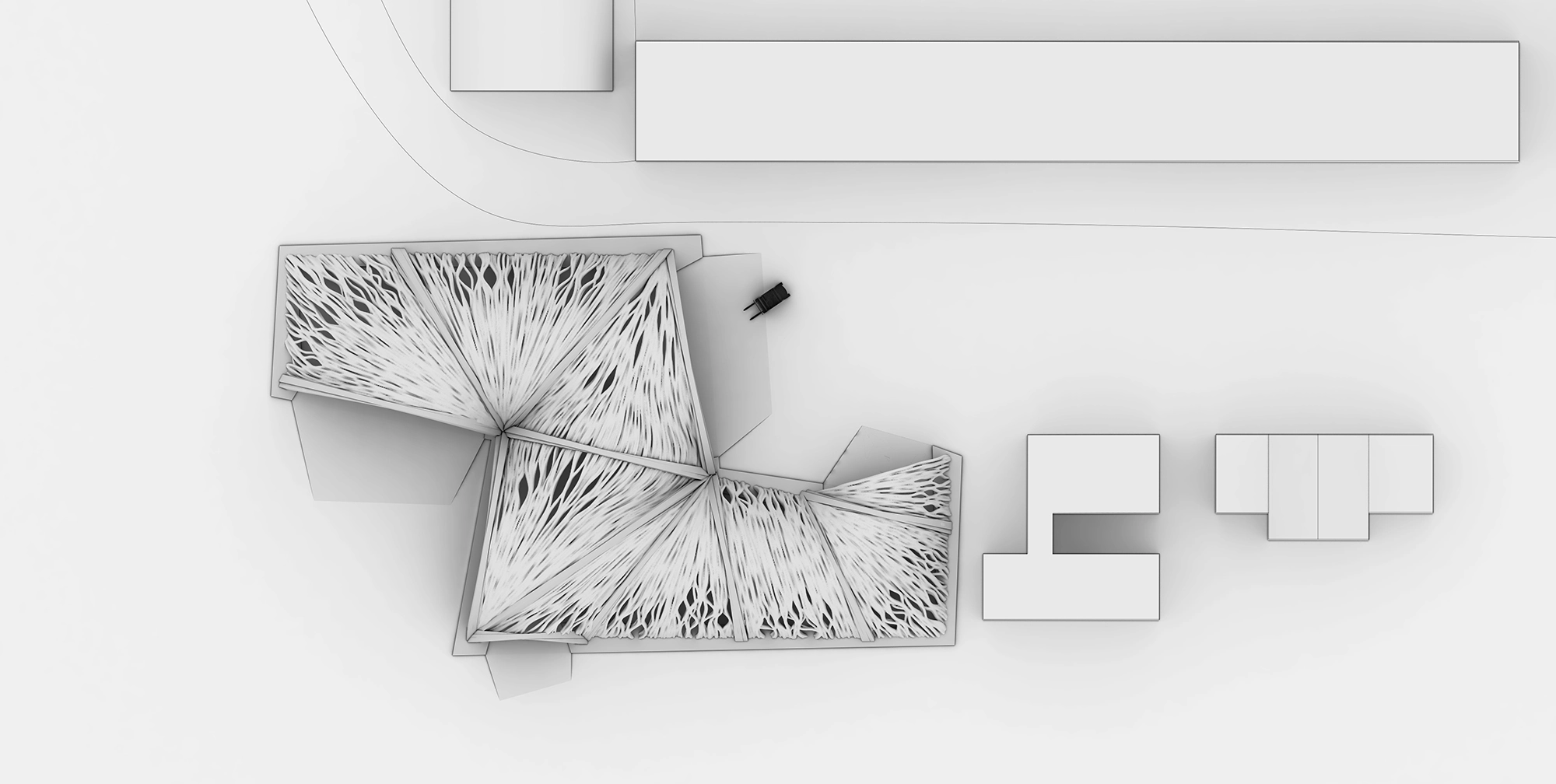
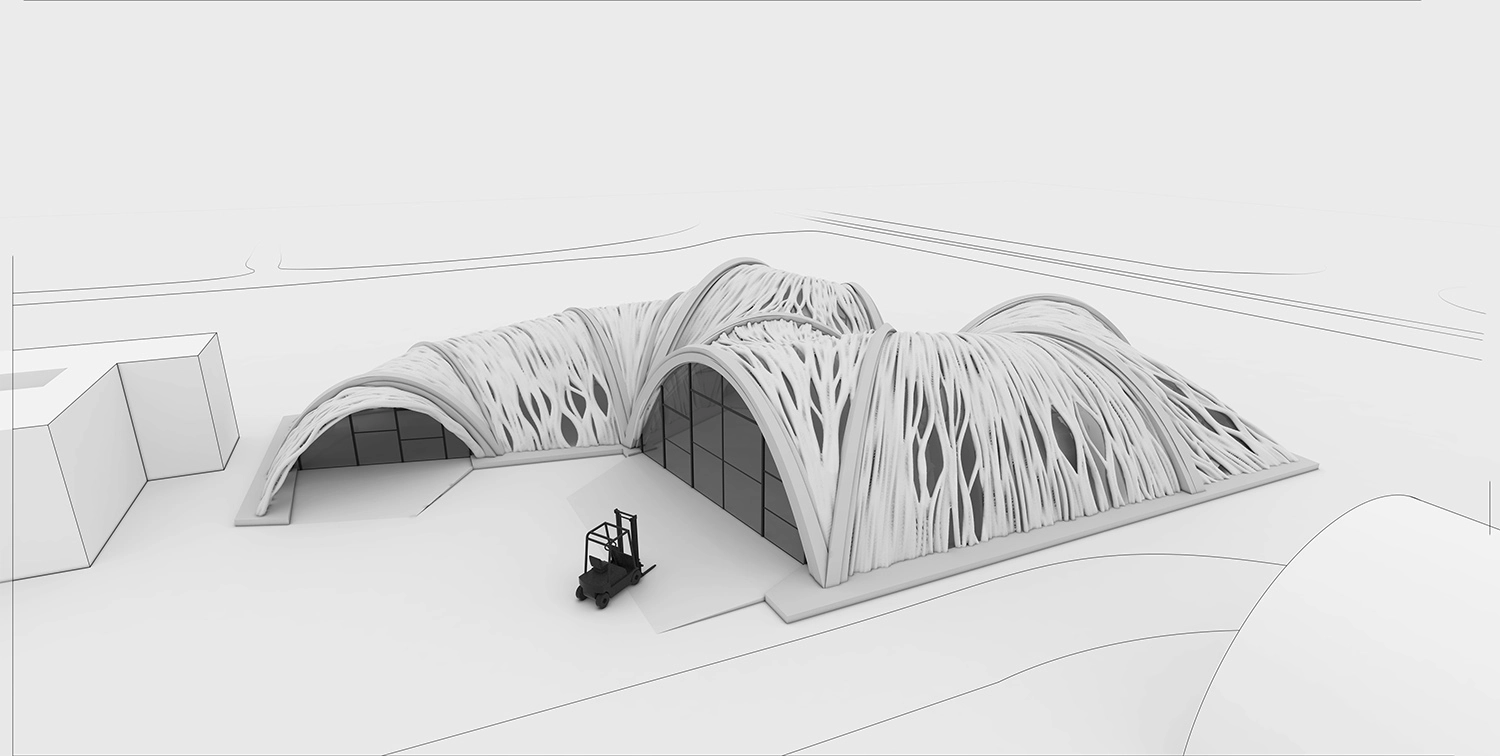
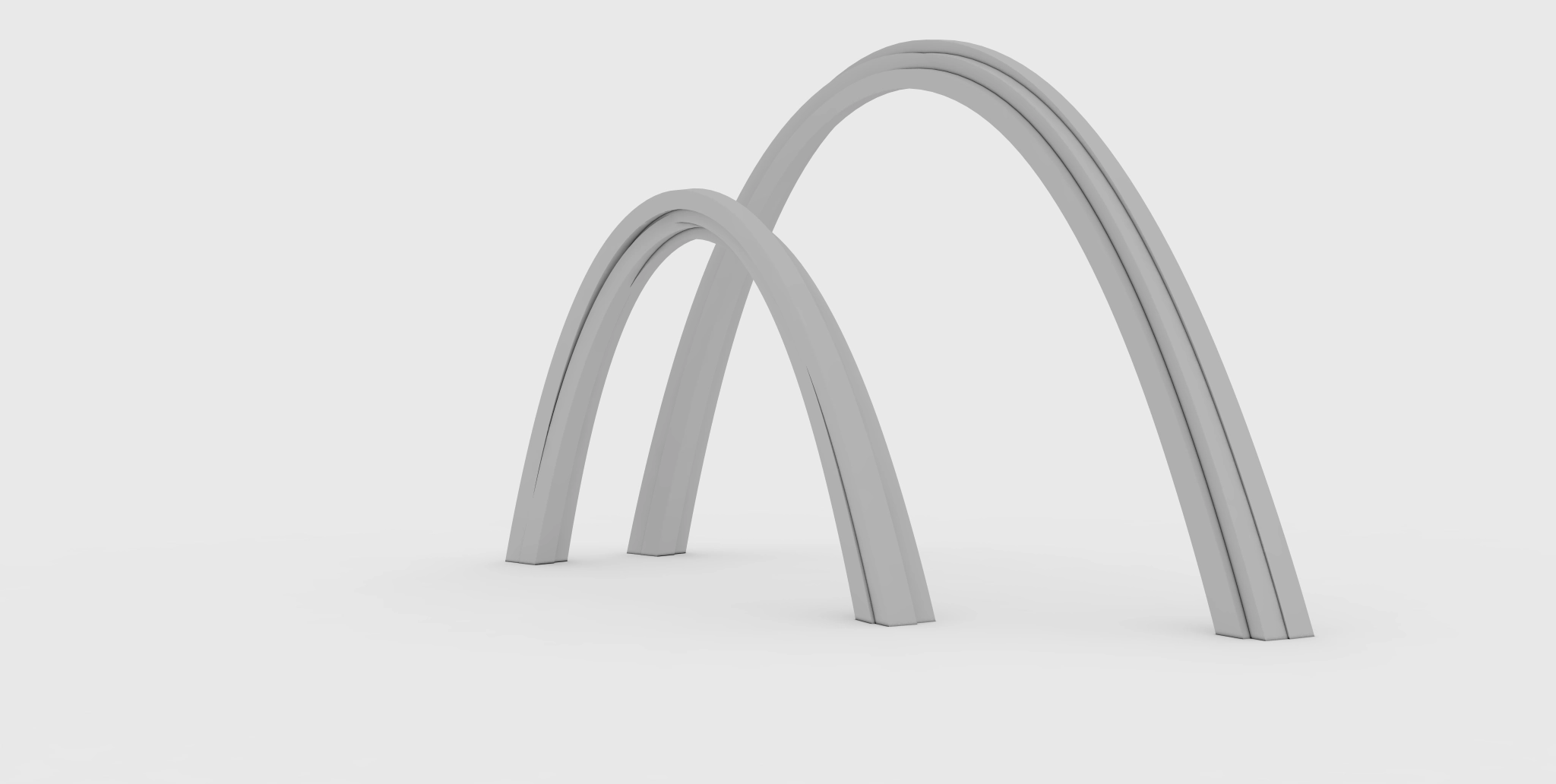
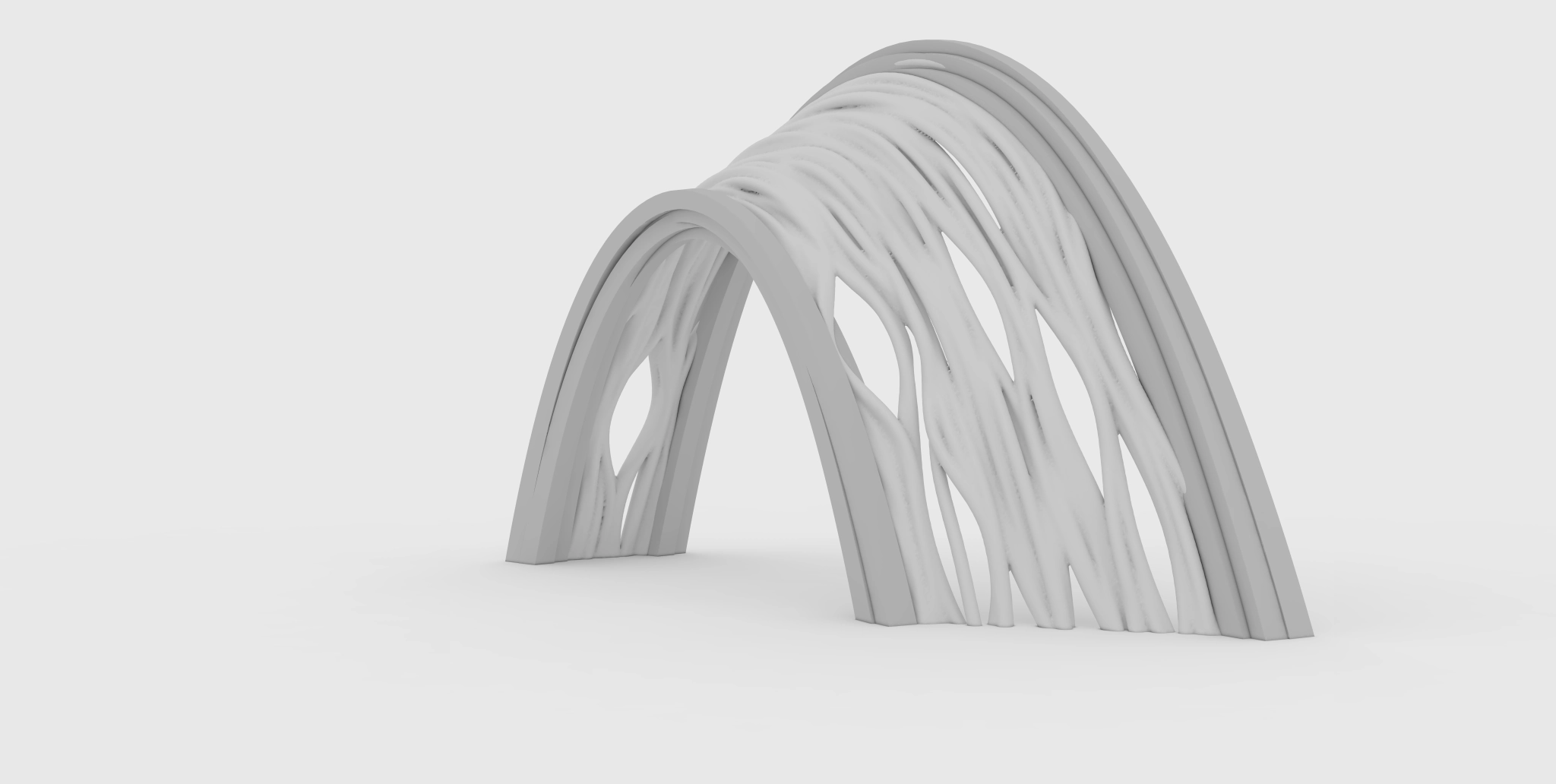
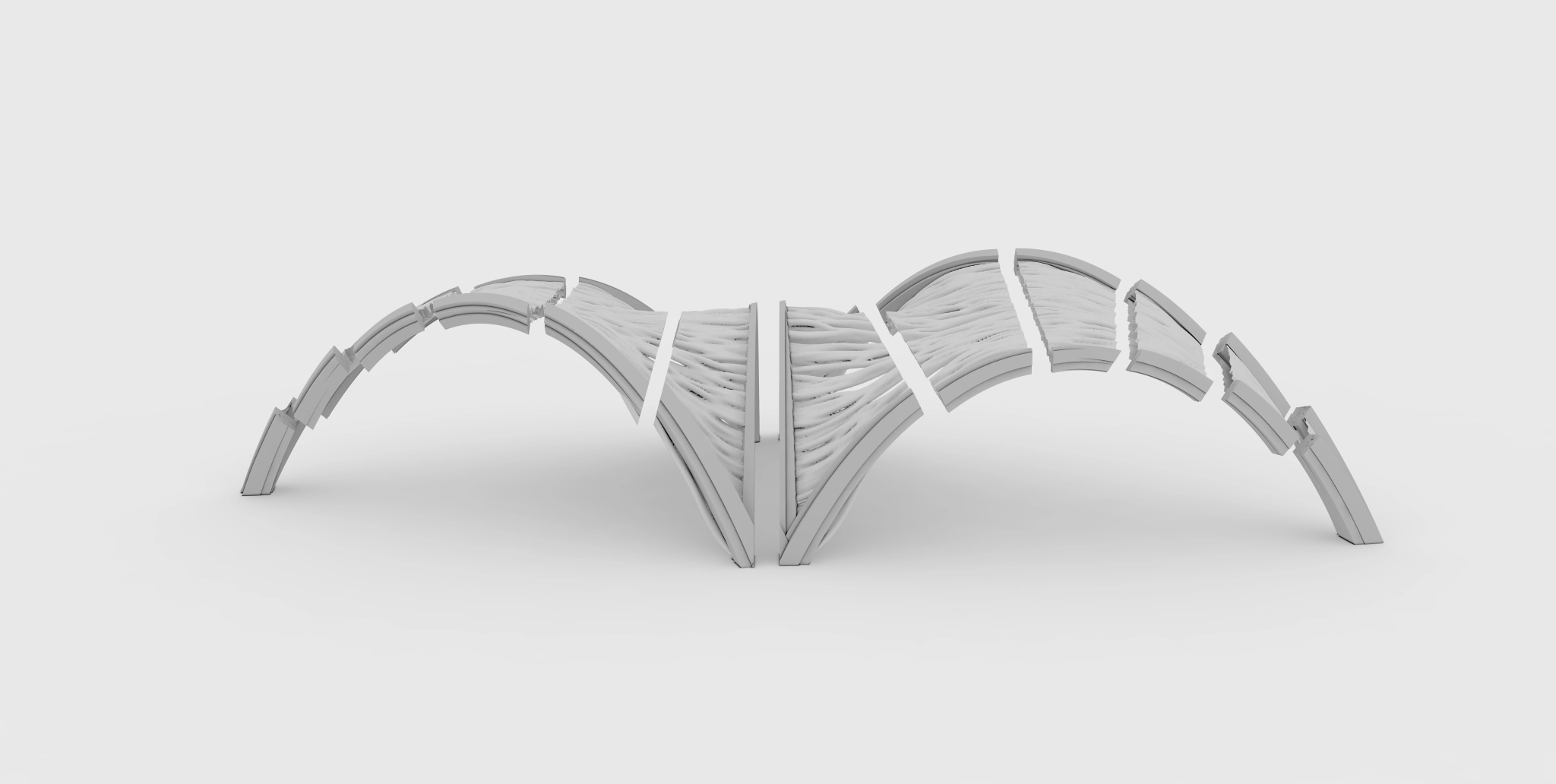
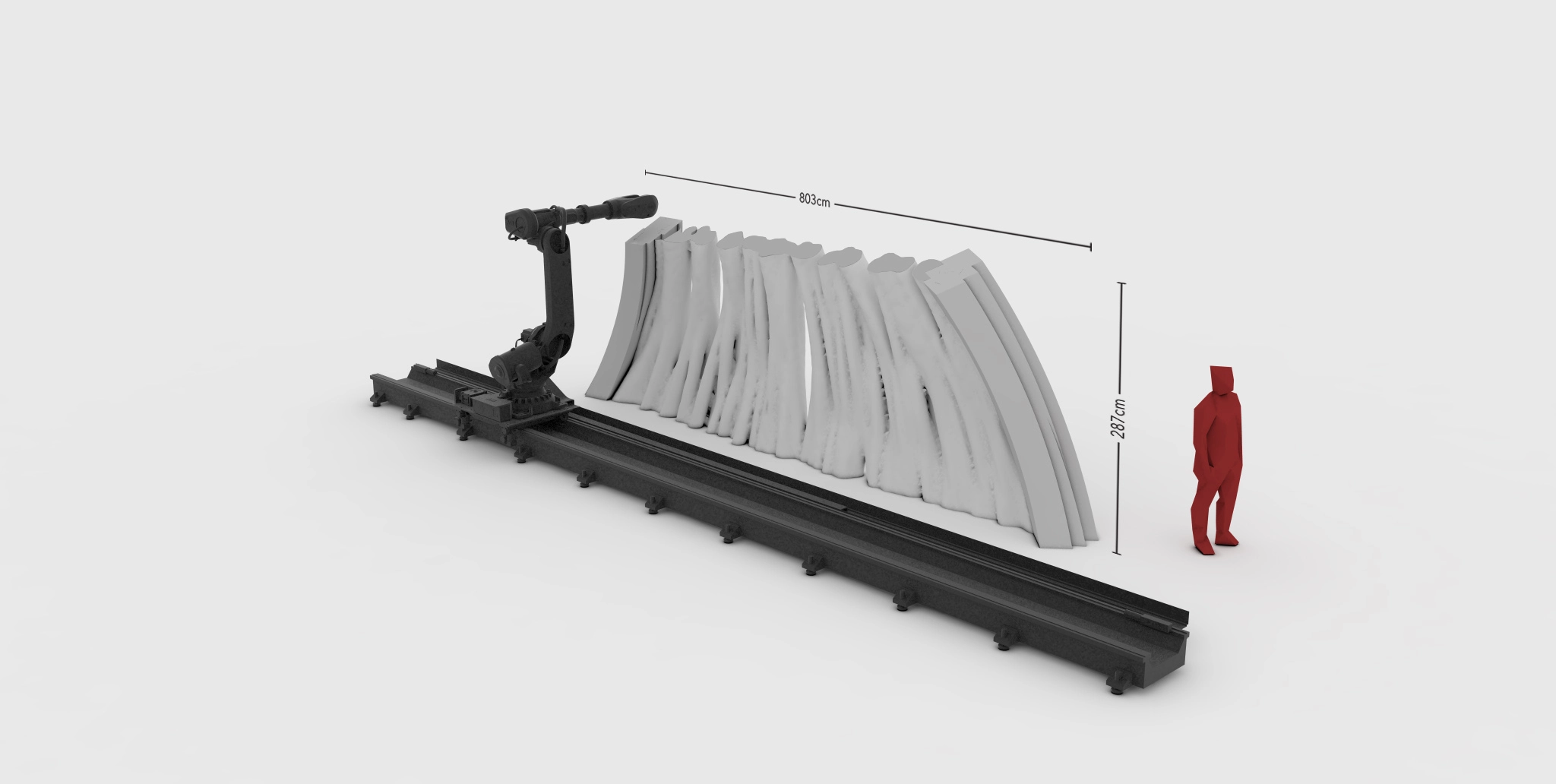
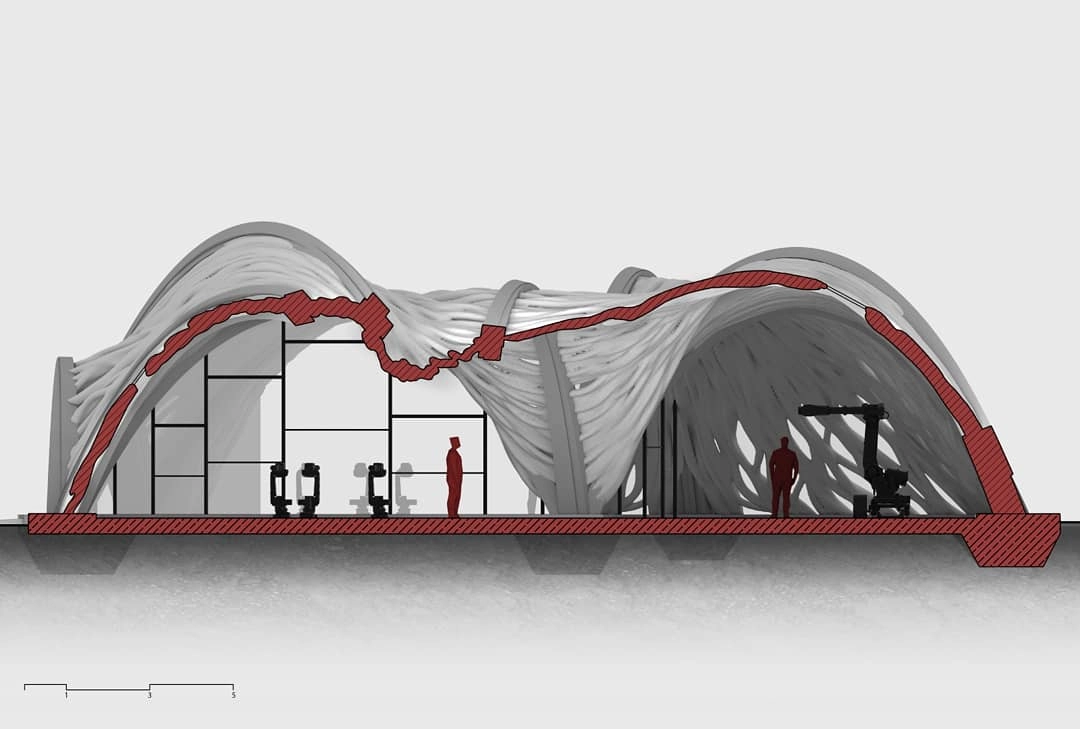
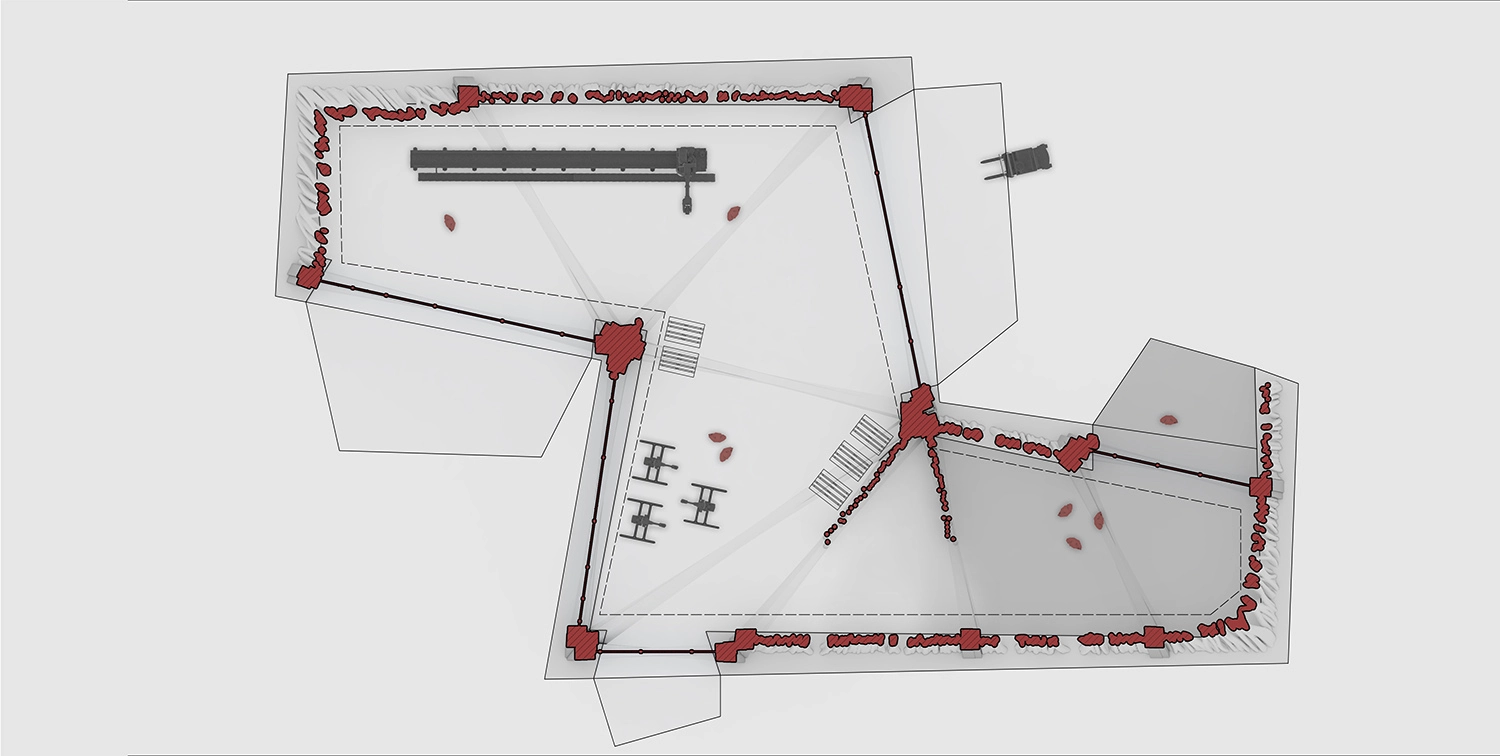
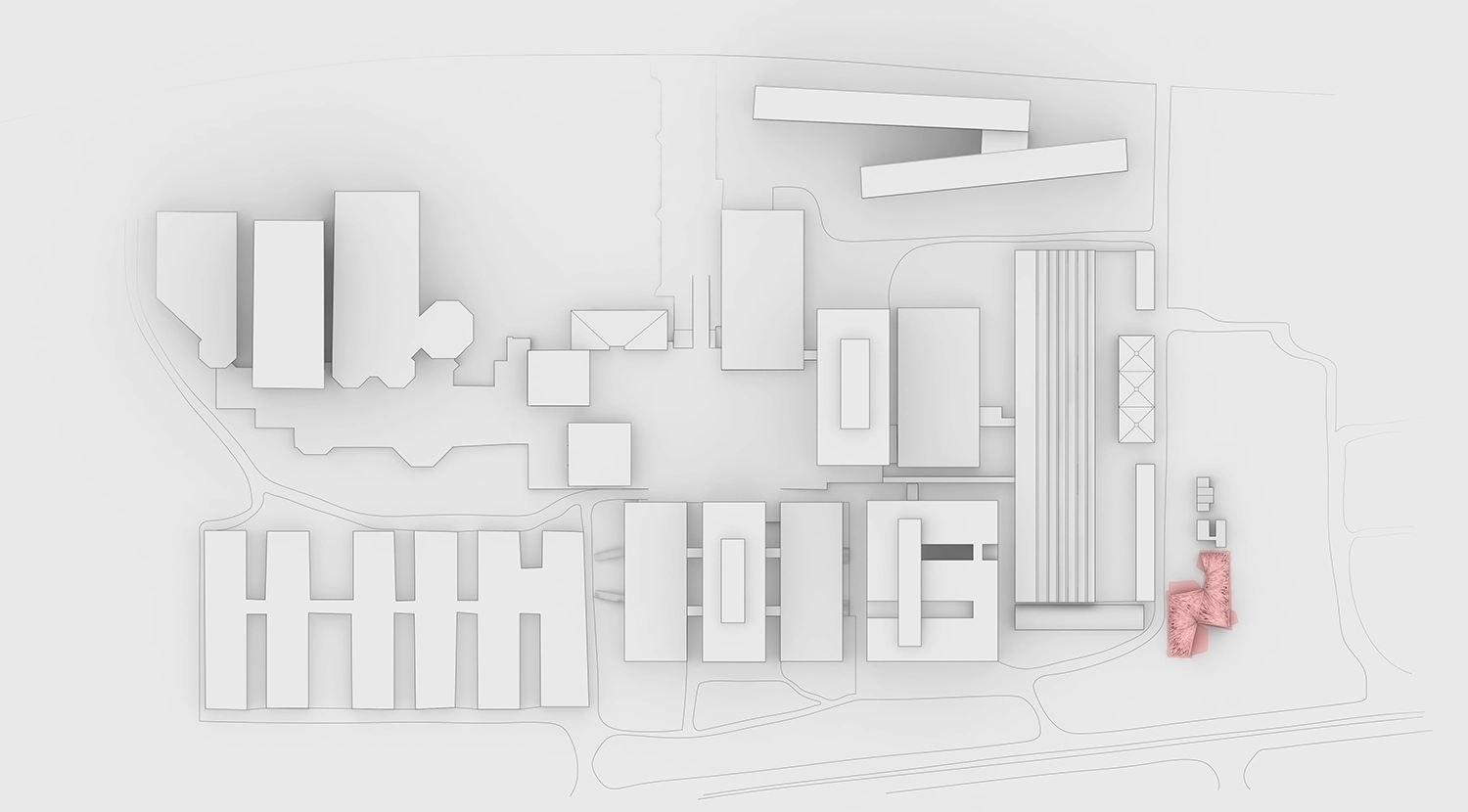